15.09.2007
Идеи Группы МАКССТОР в производство!
В последнее время в Департаменте складских технологий Группы МАКССТОР примерно половина заказов на проведение логистических исследований составляют работы для различного вида производственных предприятий.
Это и работы по созданию новых производственных систем, где склад является равноправной составляющей, либо работы по реконструкции уже существующих, где ранее во-просам организации складского хозяйства не уделялось должного внимания, что, в принципе, совершенно неверно, так как все элементы цепи «поставщики – склад сырья/комплектующих – производство – склад готовой продукции – потребители» одинаково важны для эффективного функционирования производственной системы в условиях неравномерности поставок/отгрузок, изменения ассортимента и т.п.
Склад дает возможность производству иметь необходимые ресурсы для выпуска продукции в течение задан-ного промежутка времени, обеспечивать определенные запасы для хранения готовой продукции при снижении реализации, то есть сделать работу любого производства более гибкой и стабильной. Для нас это положительный момент, так как появился устойчивый поток разнообразных интересных заказов, с другой стороны, это выгодно и конечному потребителю, так как может существенно снизиться стоимость товаров.
Почему?
Нам много раз приходилось наблюдать, когда на складах сырья и комплектующих исходные компоненты складывались на «свободное место» (см. рис.1). В результате образовывались недоступные завалы и найти что-то нужное для производства было просто невозможно либо требовало много времени. Иногда старые запасы обнаруживались после нескольких недель!
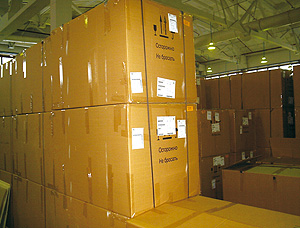
Рисунок 1.
А для выполнения производственной программы приходилось вновь изготовлять/приобретать необходимые компоненты. Естественно, это существенно сказывается на себестоимости продукции. Какой уж тут принцип FIFO!
В Группе МАКССТОР прекрасно понимают важность отмеченной проблемы, так как мы имеем богатый опыт выполнения заказов для химической, машиностроительной, легкой и пищевой промышленности по реорганизации складов.
Для примера приведем проект реорганизации складского хозяйства предприятия, для которого решалась задача переоснащения склада без остановки производства с минимальными разовыми инвестициями и с повышением уровня автоматизации складских и производственных процессов. Концепция разрабатывалась для уже существующих помещений, в которых находился производственный блок.
Производственно-складской комплекс располагался в одном здании. Производство, оснащенное современным технологическим оборудованием, в другом с зонами приемки, хранения и отгрузки. Первоначально на складе для хранения исходных компонентов и готовой продукции предусматривалось только напольное хранение (см. рис.2).
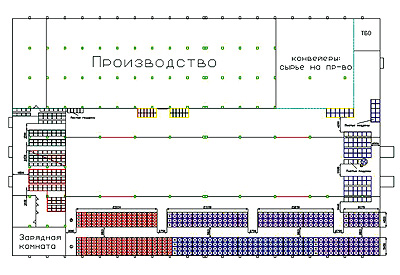
Рисунок 2.
Грузы поступали и отправлялись с торцевых сторон здания через ворота с перегрузочными мостами. На прилегающих площадях производилась первоначальная переработка поступающих товаров, например, паллетирование. Компоненты (после приемки) и готовая продукция (после изготовления) помещались на пол (иногда в несколько ярусов) в центр помещения на свободное место (достоинства подобного способа хранения уже описывались выше). Даже после первого осмотра помещения можно было сделать вывод о том, что площади и объем склада используются нерационально.
Поэтому руководство предприятия поставило задачу разработать новую логистическую складскую концепцию и определить потребности в складских помещениях при планируемом увеличении объема производства. Если исходить из того, что выпуск готовой продукции должен происходить без остановки производства, то, очевидно, что переоборудование склада необходимо было проводить в несколько этапов.
На первом этапе решалась задача переноса зон хранения сырья и готовой паллетированной продукции на другие площади, оборудованные набивными стеллажами глубиной 6 и 5, также 4 и 3 паллеты (для паллет разного размера). Сам ввод в эксплуатацию набивных стеллажей не влияет на ход производственного процесса, так как предполагается постепенное перераспределение функций между центральной частью помещения и выделенных площадей под набивные стеллажи. Площадь центральной части была выделена под хранение и отбор исходных компонентов.
И на начальной стадии реорганизации (без увеличения роста объема выпуска) появилась возможность упорядочить хранение и отбор остальных исходных компонентов. Затем постепенно в два этапа было проведено переоборудование центральной части помещения, для которой наиболее целесообразным оказалось использование фронтальных паллетных стеллажей.
В итоге нам удалось организовать сопряженный с производством склад, обеспечить адресное хранение грузов и решить вопросы разграничения ответственности за материальные ценности при поступлении грузов на хранение и выдачи их на производство. Окончательный вариант планировки склада показан на рисунке 3.
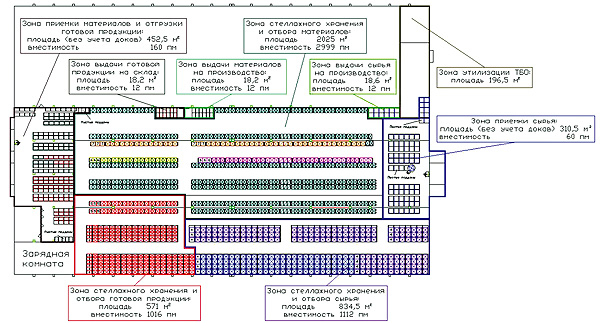
Автор: В.А.ЗУЕВ, к.т.н., доцент, Директор департамента складских технологий, С.В.ДУНАЙЦЕВ, менеджер проекта
|